The spec was a ‘book of random and very old pages of varying sizes (loose, bound and scrolls), bound in animal skins. Everything should look like what could be found 2000 years ago (Parchment, scraps etc). And a prominent and specific logo on the front.’ This I could work with.
The first step was to test a few paper weathering techniques. I tried coffee, tea and a few other things, but settled on a super strong tea brew bath. Normal paper bathed in the weathering solution was a fail, but scrunched and torn paper bathed in it came out looking awesome! (Note these were force dried in a small bathroom with a heater pointing at hand-made drying racks. No photos of this sorry but I can guarantee you’ve never seen anything like it!)
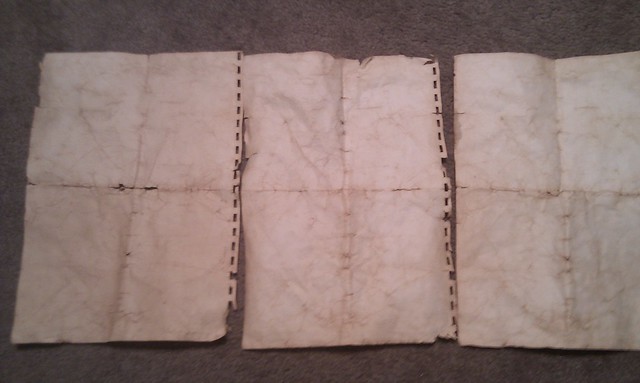
Then the other tests, the logo, the stitching and the weathering. In hindsight, using leather dye on fur is a bad thing… Or perhaps Kangaroo fur has certain properties, further testing is needed hehe.
PSA: don’t put kangaroo fur in the oven :D
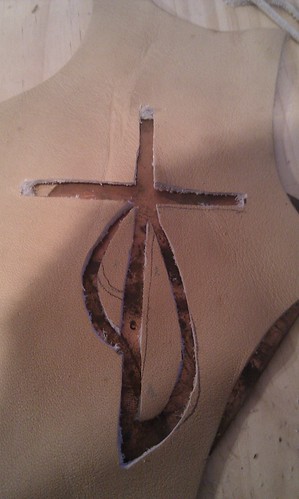
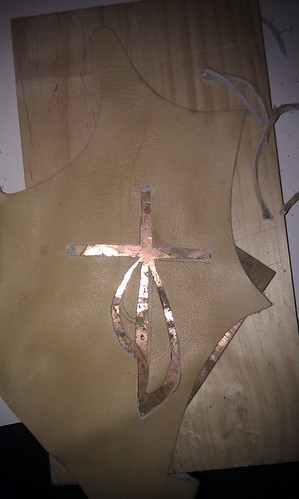
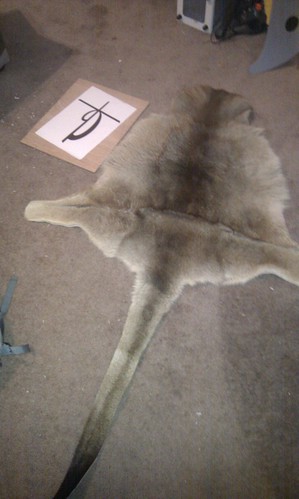

Once I had enough paper to make a small book and all the other methods down pat, I started researching book binding techniques as I wanted it as book-like as I could, while keeping with the spec. This involved cutting the book cover boards to size and laying everything out ready.
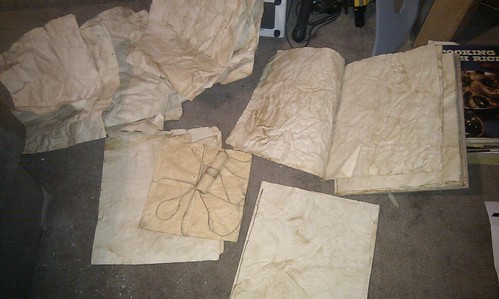
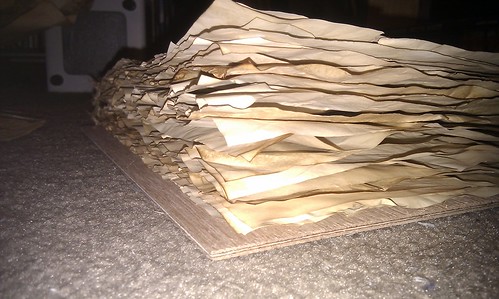
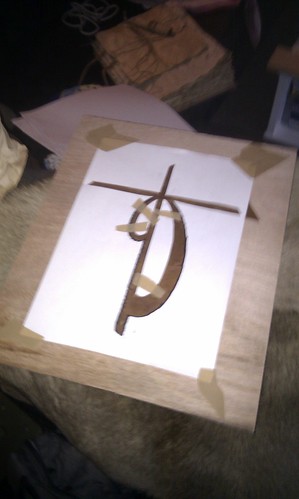
I folded small stacks of paper in half (for a specific size end result), poked holes through and tied them together with twine.
Then I bound the small stacks together with more twine. When I had about 10 or so stacks I started stitching them together over short lengths of rope for the raised spine ridges. These were then all joined together in various ways (paper stitched to the rope, holes through the cover boards for the rope to be glued, cover papers glued to the inside.)
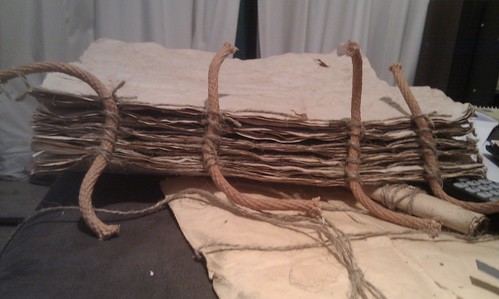
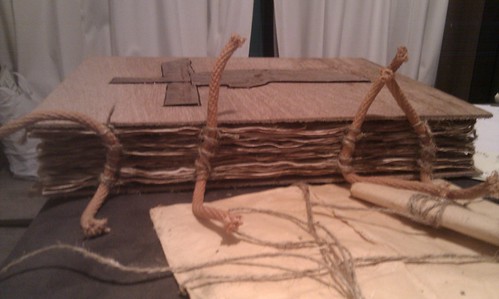
For the logo I tried various ways of laying leather over it, but settled on cutting the logo out directly and having some textured copper plate show through. The copper was weathered with vinegar, lemon and salt to bring out the green patina.

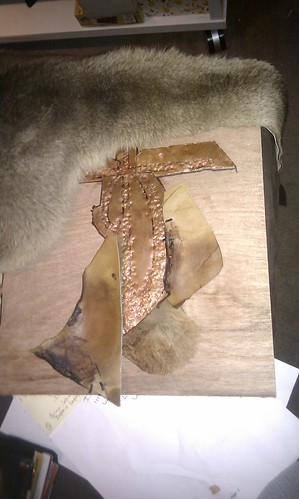
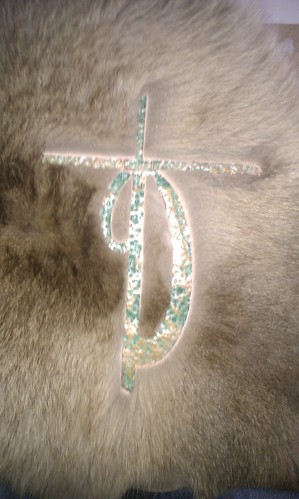
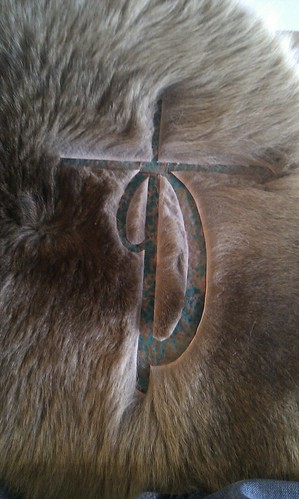
At this point I had my own version of the Harry Potter book The Monster Book of Monsters (By Edwardus Lima). So much fur! This had to be fixed.


I tried to hand cut the fur back with scissors, with clippers but it all left obvious lines cut into it. I wracked my brain for a few days and finally came up with a way of weathering the leather while taking the fur back! A heat gun and mouse sander. The heat gun was used to burn and singe the fur which caused it to go brittle, then I used the mouse sander to sand the fur off down to the leather. This helped with the weathering too as it blackened everything and cooked it all in place. You can see the areas on the spine where the ridges showed through.
(I will never again complain about sanding dust, as smelling like burnt, wet, old fur is one of the worst things I’ve experienced. I believe I was banned from the house until I was hosed clean up against the wall.)
And finally I used some metal wire (it wasn’t brass or copper as it was quite soft) to ‘sew’ the leather down to the board through drilled holes. This was also weathered with some acrylic paint around the holes to tie it all together. (Sorry for the quality of photos, my camera died and had to rely on phone cameras.)

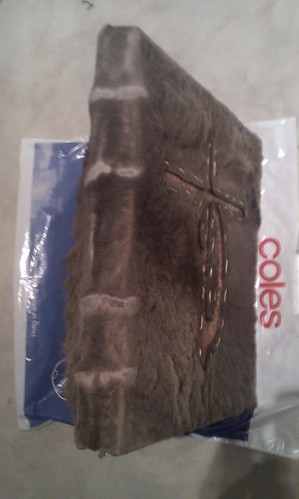
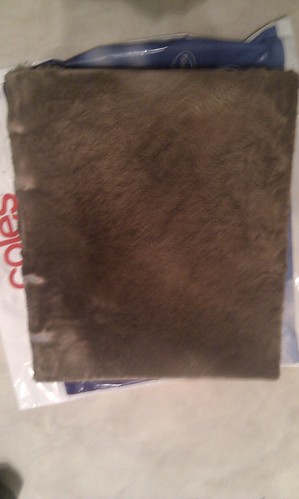
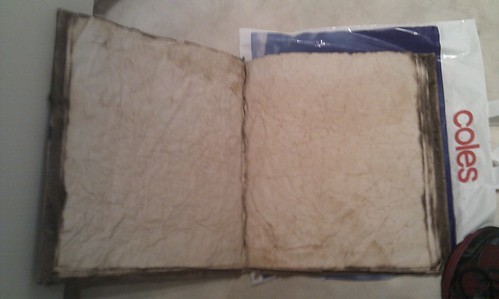
And voi la! A completed 2000 year old book! (Woops, forgot to remove the cut out logo..) Final photo by Cole Bennetts.
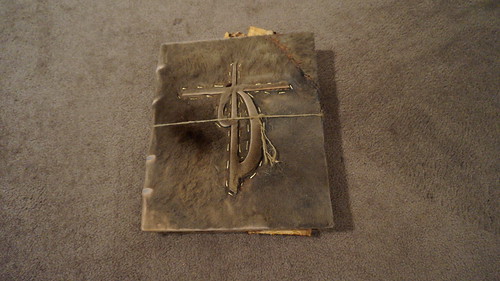
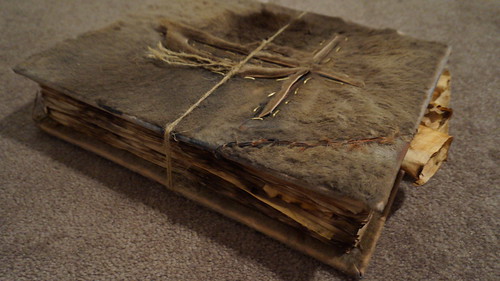
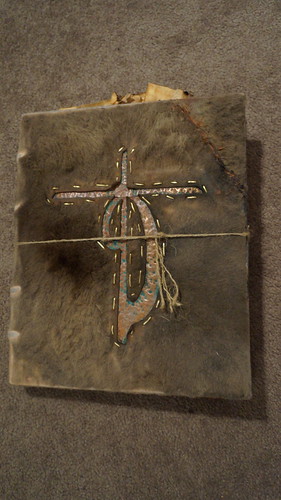
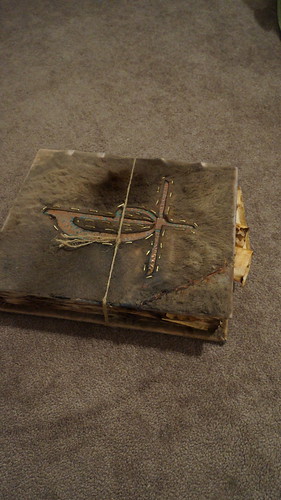

links
https://www.facebook.com/scottbakerauthor/?fref=ts
http://www.ruleofknowledge.com/
http://www.goodreads.com/book/show/18341315-the-rule-of-knowledge
http://www.amazon.com.au/The-Rule-Knowledge-Scott-Baker-ebook/dp/B00C2PEFWU
http://blog.booktopia.com.au/2013/08/20/matthew-reilly-recommends-the-rule-of-knowledge-by-scott-baker/